Development of a novel method for investigation the uptake behaviors of acid dye on silk fabric at various flow statuses in a coloration circular pipe
⁎Corresponding author. longjiajie@suda.edu.cn (Jia-Jie Long)
-
Received: ,
Accepted: ,
This article was originally published by Elsevier and was migrated to Scientific Scholar after the change of Publisher.
Peer review under responsibility of King Saud University.
Abstract
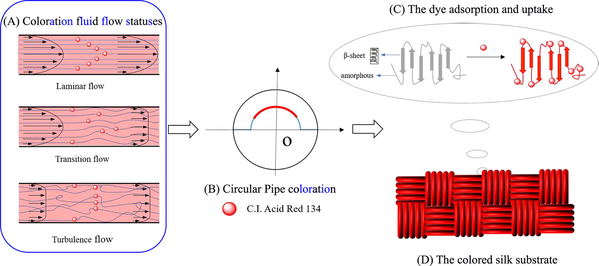
Abstract
-
A special dynamics coloration machine was successfully built for coloration for the first time.
-
A novel methodology was further constructed to investigate dye uptake behavior on silk.
-
Various uptake behaviors of an acid dye on silk were disclosed in different flow statuses.
-
Coloration in laminar and transitional flow prefers a low dosage of neutral salt in bath.
-
Appropriate control of dyeing flow statues is beneficial to an efficient cleaner production.
Abstract
A novel methodology and a special fluid dynamics coloration machine were successfully constructed, and then the uptake behaviors of an acid dye on silk fabric under different flow statuses and parameters were explored for the first time. The obtained results show that the traditional additions of auxiliaries will not significantly change the kinematic viscosity of the dyeing bath. As coloration flow status was in laminar, transitional and turbulent flow, respectively, the dye uptake behaviors on the silk fabric were significantly different. Meanwhile, decreasing the bath pH value and increasing the temperature of the dyeing bath had a significant positive effect on the dye uptake behaviors in different flow statuses. Additionally, coloration in laminar or transitional flow preferred a relatively low dosage of neutral salt, which benefits to a cleaner production. Additionally, high coloration performance with color-fastness to washing and rubbing of the dyed silk at 4-grade or above was achieved under different flow statuses. The results further clearly indicate that the constructed method and self-built fluid dynamics coloration machine are helpful to investigate dye uptake behavior in different flow statuses, and are potentially beneficial to an efficient process and parameters design for cleaner production in textile coloration.
Keywords
Uptake behavior
Coloration methodology
Flow status
Fluid dynamics coloration machine
Silk fabric
Acid dye
1 Introduction
In recent decades, with the development of the textile industry, environmental pollution has become increasingly severe (Chen et al., 2019; Liu et al., 2021; Hasanbeigi and Price, 2015). At the same time, with the increasingly strict environmental protection legislations and improved environmental protection awareness, how to reduce the use of auxiliaries and minimize the discharge of dyeing wastewater accompanied with maintaining or even improving coloration performances, has become the focus of research (Ozturk et al., 2016; Xiao et al., 2017; Library, 2017). Accordingly, a series of environmentally friendly coloration methods, such as supercritical carbon dioxide dyeing, photocatalytic technology, etc., have been successfully developed and investigated for the green and sustainable manufacturing of textile products (Long et al., 2012, 2014,2015; He et al., 2021; He et al., 2019). Moreover, as regards to traditional textile dyeing methods, the influences of dyeing performance or dye uptake behavior on textile substrates during a process from various parameters, such as dyeing temperature, dyeing duration, pH value, the amounts of auxiliaries, have become a key point for applications in practice as well as the hot topic of academic research (Tzanov et al., 2003; Guo et al., 2020; Chairat et al., 2005; Zhang et al., 2020). However, during the conventional textile dyeing processes, particularly for those exhausting processes, the influences from the flow statuses of aqueous dyeing media or its Reynolds number on the dye uptake behavior or dyeing performance onto textile substrates are often ignored easily and very lack in the literature, even though it is very important to design and control an efficient coloration process along with energy conservation and discharge reduction.
Theoretically, the flow status of a fluid can be divided into typical three types, laminar flow, transitional flow and turbulent flow, according to its Reynolds number (Lin, 2013). Reynolds number (Re) is a dimensionless physical quantity, as shown in formula (1), which is proportional to the average flow velocity (u) in the cross section of a fluid and the characteristic diameter (d) of its flowing pipe, and inversely proportional to the kinematic viscosity (ν) of the fluid (Pavelyev et al., 2003). Generally, as for circular pipe flow, the fluid is in laminar flow status as its Reynolds number is less than 2300, then a transitional flow status could be observed as its Reynolds number is between 2300 and 4000, and finally a turbulent flow could be further achieved as the Reynolds number is over 4000 according to the Nicholas curve and Modi diagram (Lin, 2013).
In a laminar flow, the influence of viscous force is greater than the inertial one on its flow field, and the viscous force plays a dominant role in the actions of the fluid micro mass (Lin, 2013). Under the action of viscous force, the disturbance of the fluid in the flow field is attenuated, and the flow is in a stable state. The micro mass in this kind of flow moves along a smooth straight line paralleling to the pipe axis, and there is no obvious irregular pulsation in the trajectory of the fluid micro mass. There is only momentum transfer caused by molecular thermal motion and no mass transfer between adjacent fluid layers (Javed et al., 2020; Guha, 2008). However, in a turbulent flow, the influence of inertial force is greater than viscous one on its flow field, and then the inertial force plays a dominant role in the actions of the fluid micro mass and/or micro clusters (Lin, 2013; Annus and Koppel, 2011(20); Mullin, 2011). In this case, the fluid micro mass and/or micro clusters not only have lateral pulsations but also reverse their motions which are mainly contributed to the total motion of the fluid. Therefore, the trajectory of the fluid micro clusters is extremely disordered and changes rapidly in a turbulent flow. There is not only dose momentum transfer occurred in the turbulent flow, but also heat and mass transfer simultaneously happen between their adjacent fluid layers, and the transfer rate is several orders of magnitude higher than that of laminar flow (Afzal et al., 2020). Transition flow is a kind of flow status between laminar and turbulent flow, and the motions of fluid micro clusters are more complex than laminar and turbulent ones (Lin, 2013; Mullin, 2011). Therefore, different flow statuses of coloration fluid could readily lead to different motions of the fluid micro clusters, ions and/or molecules of dyes and auxiliaries in the dyeing bath, which could remarkably impact on the dye uptake behavior and performance onto the textile substrate. Particularly, Etters (Etters, 1995) also pointed out that the diffusion rate of a dye was greatly affected by the dyeing liquid flow status. Krichevsky (Krichevsky, 1985) further indicated that the diffusion rate of a dye mainly depended on the dyeing liquid flow rate. Consequently, to control an appropriate dyeing liquid flow status is the most direct and simple way to facilitate an efficient uptake process on the fabric.
Up to date, many methodologies and some parameters have been developed and investigated to overcome the influences and/or reasonably utilize the coloration fluid flow statuses for an efficient mass and a heat transfer in dyeing bath to achieve satisfactory colorations in actual production processes. Mahdi (Mahdi et al., 2020), Luepong (Punyachareonnon et al., 2021), Adeel (Adeel et al., 2020), Mansour (Mansour and Heffernan, 2011) and Boonla (Boonla and Saikrasun, 2013), etc., explored the effects of temperature, pH value, auxiliary concentration, and other factors on the dye uptake behavior on silk, and successfully developed a series of dyeing methodologies for silk, such as plasma, ultrasonic, and microwave assistant coloration methods. Although these researches have successfully improved dye uptake behaviors on silk substrate to some extent, there are still some defects needed to be improved further, such as complicated dyeing procedures and a relatively large amount of auxiliary agents involved. Moreover, among all those methodologies, the control of fluid flow status is a basic, direct and efficient method to alter and improve the mass and heat transfer for coloration, as well as to conveniently adjust the thickness of the diffusion layers in dyeing bath. But unfortunately, up to now, there is no any professional, suitable method and efficient equipment or machine to investigate or explore the uptake behaviors of dye molecules conveniently in different flow statuses in dyeing baths, as well as the influences from system parameters.
The purpose of this work is to construct a novel methodology and a special fluid dynamics coloration machine equipped with a circular pipe for conveniently and efficiently investigating and exploring the uptake behaviors and performances of an acid dye on silk fabric for the first time in different fluid flow statuses, as well as in order to construct or develop some possible basic knowledge for sustainable and cleaner production in textile coloration. Simultaneously, the influences of various parameters for different fluid flow statuses, such as Reynolds number, pH value, temperature, application of anhydrous sodium sulfate and peregal O, were also investigated and optimized for the development of cleaner production in textile coloration.
2 Experimental section
2.1 Materials and chemicals
A pure silk fabric with a specification of 65.0 g m2 and a plain weave, which was fully bleached and degummed, was used in this work. A commercial acid dye (C.I. Acid Red 134) was utilized for silk dyeing in this work, which was kindly supplied by Shanghai Anoqi Group Co., ltd. (Shanghai, China) and its molecular chemical structure was depicted in Fig. 1. The commercial peregal O (fatty alcohol Polyoxyethylene ether O) was supplied by Wuxi Yatai United Chemical Co., ltd. (Wuxi, China). Other chemicals, such as anhydrous sodium sulfate, disodium hydrogen phosphate dodecahydrate and citric acid monohydrate, used in this work all were analytical pure grade and purchased from Sinopharm Chemical Reagent Co., ltd. (Shanghai, China).
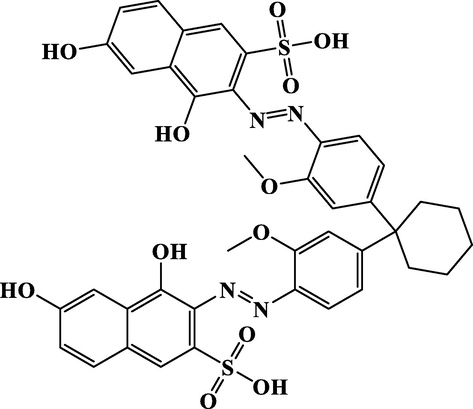
- The chemical structure of the employed C.I. Acid Red 134 dye.
2.2 Apparatus and procedures
2.2.1 Development of fluid dynamics machine and the uptake of acid dye on silk in various flow statuses
As shown in Fig. 2, the development of the coloration machine was mainly composed of a pump (10), a regulator box at the top (4), a reservoir at the bottom (1), a coloration circular pipe (7), a proportional valve (8) and a flow meter (9), etc. As the pump was working, the coloration fluid in the reservoir could be transported up to the regulator box and then flowed through the coloration circular pipe with a constant fluid level difference to maintain the stability of the fluid during a coloration process. Furthermore, the proportional valve was employed to control the flow velocity of the coloration fluid in the circular pipe, and the flow meter was used to accurately measure the corresponding flow velocity of the coloration media passed through the circular pipe.
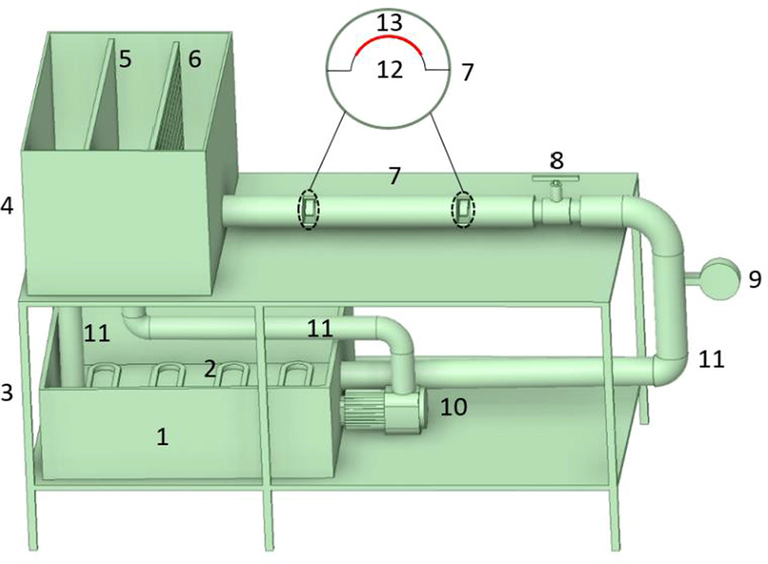
- Schematic diagram of the self-built special fluid dynamics coloration machine for silk dyeing. (1): Reservoir; (2): Heating unit; (3): Shelf; (4): Regulator box for coloration fluid; (5): Overflow plate; (6): Steady flow plate; (7): Coloration circular pipe; (8): Proportional valve; (9): Flow meter; (10): Pump; (11): Circular pipe; (12): Fabric strip holder in a concentric semicircle shape; (13): Silk fabric strip.
Meanwhile, a series of the lamelliform holders in a concentric semicircle shape with a radius varying from 10.0 mm to 2.5 mm were made and set in the coloration circular pipe according to a specific experimental requirement with a distance varying from 7.5 mm to 15.0 mm from the pipe inner wall, respectively, as shown in Fig. 2. Then a silk fabric strip in a dimension of 70.0 × 1.5 cm (Length and width) was fixed on the arc-shaped holder for performing a dye uptake process. Therefore, a utilized Reynolds number on the fabric strip surface could be equal everywhere in a predetermined circular pipe flow layer during an uptake process.
Accordingly, the uptake process of the acid red dye 134 on silk fabric was carried out in the self-built special fluid dynamics coloration machine as follows. After preparation for the dyeing bath according to the recipe of silk fabric coloration (namely, a certain amount of anhydrous sodium sulfate and peregal O with the presence of the acid red dye at 0.05 g/L in 200 L aqueous bath, along with pH value at 5.0 with for 30.0 min duration), the dyeing bath was then heated to a predetermined temperature, and was continuously elevated and charged into the regulator box from the reservoir by the pump. As the liquid level of the coloration fluid reached the maximum height of the overflow plate to meet experimental request, the proportional valve was switched on and adjusted to a required value, particularly to realize a coloration process under different flow statuses or Reynolds numbers, as shown in Scheme 1 (A, B). Then the aqueous coloration fluid in the regulator box was flowed through the coloration pipe circularly under constant pressure and formed a stable, predetermined flow status for a hydrodynamic coloration process. Thus, the acid red dye molecules or ions as well as the employed auxiliaries in the coloration solution could adsorb and uptake onto the silk fabric strip on the arc-shaped holder via their various interactions, as the fluid was flowing through the coloration pipe with a controlled flow status and other conditions, as shown in Scheme 1 (B, C, D). Finally, after the requested coloration duration, the silk fabric strip was taken out and fully rinsed with tap water to remove some excess dye molecules, auxiliaries and other impurities on the fabric substrate. Then the colored fabric samples were dried in air at a room temperature and conditioned at 25.0 °C with a relative humidity of 60.0 % ± 5.0 % for 24.0 h before further measurements.
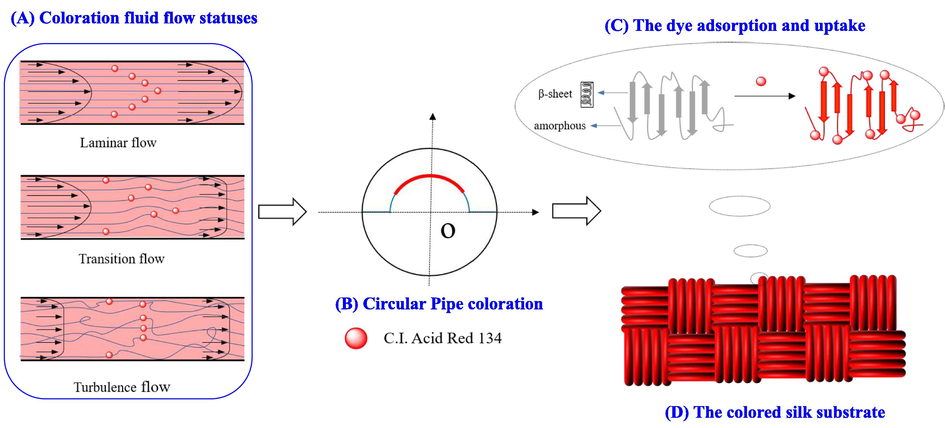
- Schematic diagram of the circular pipe dyeing of silk fabric in different flow statuses by employing the self-built special fluid dynamics coloration machine: (A) coloration fluid flow statuses, (B) circular Pipe coloration, (C) the dye adsorption and uptake, (D) the colored silk substrate.
2.2.2 Measurement of kinematic viscosity for the employed aqueous coloration fluid
The kinematic viscosity (ν) of the employed aqueous coloration fluid was measured at 27 °C by employing an ubbelohde viscometer (Shanghai Liangjing Glass Instrument Co., ltd., China), in which the inner diameter of the capillary is 0.3–0.4 mm. The coloration fluid media mainly involved a dosage of the acid red dye at 0.05 g/L, 0–20 g/L of anhydrous sodium sulfate and 0–0.8 g/L peregal O. A duration(t)for the coloration fluid to flow through a certain height in the capillary was accurately measured by a stopwatch, and then the kinematic viscosity of the coloration fluid could be calculated according to the equation (2) and the known viscometer constant(K, K = 0.002472 mm2/s2 in this work)(Hughes and Rhoden, 1969).
2.2.3 Color measurement
The color characteristic parameters on an individual dyed silk fabric were indicated by L*, a*, b*, C*, h° values and color intensity (K/S value), which were measured on an UltraScan PRO instrument (HunterLab. Co., ltd., USA) by employing a simulated D65 light source lamp and a 10˚ visual angle with a measurement aperture at 6.6 mm. Furthermore, the color intensity (K/S value) of the silk fabric substrate was measured according to the Kubelka-Munk equation with its characteristic maximum absorption wavenumber (λmax) at 570.0 nm for the acid red dye (Guo et al., 2020; Long et al., 2011). Each silk sample to be measured was in an 8-folded form and twelve different sites were applied to. Then, as depicted in equation (3), an average value (
2.2.4 Color fastness assessment
According to China textile criteria of GB/T 3921.1-2008A (2008; equivalent to ISO 105-C10:2006 A (1)), the wet-washing fastness assessment was carried out by employing a washing-fastness apparatus (SW-12A, Changzhou Depu textile technology Co., ltd., China) with a liquid ratio 1:50 and 5.0 g/L soap powder at 40.0 °C for 30.0 min; and an adjacent fabric of SDC Multifibre DW (product code 2115, SDC Enterprises Co., ltd., UK) was used for staining fastness assessment. Additionally, according to China textile criteria of GB/T3920-2008 (2008; equivalent to ISO 105-X12:2001), a series of rubbing fastness tests were also performed by employing a rubbing tester (Y571B, Nantong Hongda Experiment Instruments Co., ltd., China) with standard rubbing cotton cloth in dry and wet states, respectively. Then the evaluation of the rubbing fastness was further carried out by employing CTA grey scale according to China textile criteria of GB/T3920-2008 (2008).
3 Results and discussion
3.1 Investigation of the kinematic viscosity of coloration fluid with various components
Generally, the kinematic viscosity of a coloration fluid is directly related to its flow status and impacts an important influence on it in the bath. Therefore, in order to conveniently and accurately investigate the coloration fluid flow status, the influences of the main components of the coloration fluid, such as the various dosages of anhydrous sodium sulfate at 0–20 g/L and commercial peregal O at 0–0.8 g/L ranges on the kinematic viscosity, were explored and made sure at the first step, respectively, with the presence of the Acid Red dye at 0.05 g/L and a bath temperature at 27 °C. The obtained results were depicted in Fig. 3.
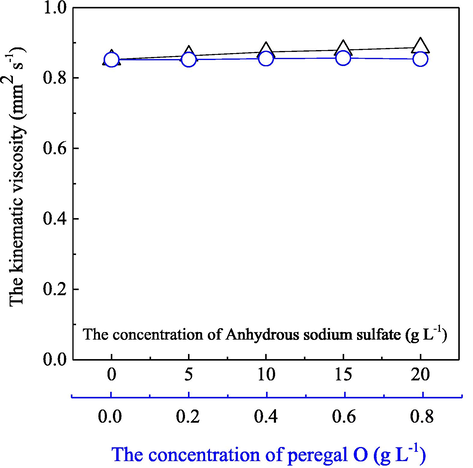
- Influence of the main components of the coloration fluid on its kinematic viscosity at a bath temperature of 27 °C with the presence of anhydrous sodium sulfate at 0–20 g/L (Δ), peregal O at 0–0.8 g/L (

Fig. 3 clearly shows that under a constant bath temperature at 27 °C, the kinematic viscosity (ν) of the employed coloration fluid showed some alterations, but did not change significantly with the presence and increase of the concentration of sodium sulfate and peregal O, respectively, in comparison with the pure water. With respect to the additions of anhydrous sodium sulfate in the coloration fluid, a weak enhancement in the kinematic viscosity (ν) from 0.853 to 0.887 mm2 s−1 was determined as the anhydrous salt increased from 0 to 20 g/L. However, almost no any influence on the kinematic viscosity (ν) from 0.852 to 0.854 mm2 s−1 was also achieved with the presence of the peregal O at a relatively low application of 0–0.8 g/L in the coloration fluid.
Theoretically, as for the absolute main component in the aqueous coloration fluid, water possesses a unique three-dimensional network structure which is constructed and maintained by numerous hydrogen bonds (Bowen and Yousef, 2003). Therefore, an internal friction resistance could be naturally and immediately occurred as some portions of water or its layers have some relative motions against the bulk, which shows an instinctive property to impede those motions from their adjacent layers or portions. It is obvious that the internal friction resistance is the original resource of the production and existence of the dynamic or kinematic viscosity (ν) in the water media or other fluids. Thus, any factors which tend to change those interactions of the water molecules and their network structures could readily impact some influences on the media viscosity, particularly for the kinematic viscosity (ν). Accordingly, with the presence and increased concentration of the sodium sulfate salt in the coloration aqueous, the more dissolved and ionized sodium and sulfate ions would enhance the polarity of the solution, and induce more polarization of those water molecules to modify and strengthen their interactions and network structures. Particularly, the hydration of one sodium ion with six water molecules would further intensify those modifications with the increased concentration of the salt in the coloration fluid. Moreover, as a typical neutral salt, the higher concentration of the sodium sulfate, the more aggregation and/or bigger microclusters of the acid red dye molecules could be occurred due to the weakened coulomb repulsions among the dye ions and/or micelles, this was also equal to intensify the inner structures of the coloration fluid. Therefore, all those possibilities resulted in the slight increase tendency of the kinematic viscosity of the coloration fluid in Fig. 3. However, the almost no change in the kinematic viscosity with the addition and increase of the peregal O shows that a nonionic surfactant, especially for a low applied dosage in the coloration fluid impacted a very less or neutral influence on the water and the coloration media structures.
Briefly, as the achieved overall results in the aqueous coloration system above, a negligible effect of the applied auxiliaries and their tested dosages on the kinematic viscosity (ν) was obtained. Consequently, a convenient, simple and practical way was employed to calculate the Reynolds numbers of various aqueous fluids for different coloration processes in this work, by utilizing the kinematic viscosity of the pure water at a corresponding bath temperature according to the equation (1) and (2). This is a basis as well as helpful to further investigate the influence of the coloration fluid flow statuses on the acid dye uptake behavior and performance on silk substrate.
3.2 The uptake behaviors of the acid dye in different coloration fluid flow statuses
In order to explore the characteristics and the influences of the coloration fluid flow statues on the acid dye uptake behavior onto silk substrate, a series of colorations were carried out at different fluid flow statuses controlled by various Reynolds numbers varying from 1000 to 12000 in the coloration pipe. The achieved results are shown in Fig. 4.
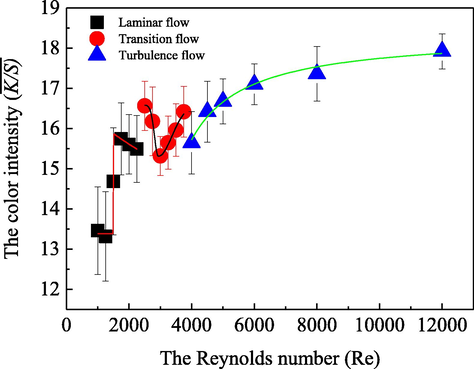
- Influence of the coloration fluid on the dye uptake behavior of silk fabric in a laminar flow (■), a transition flow (


Fig. 4 demonstrates that very different and remarkable characteristics and influences from the fluid flow statues as the Reynolds number ranging from 1000 to 12000 on the dye adsorption performances were observed. As the coloration fluid was in a laminar flow status with the Reynolds number between 1000 and 2300, the silk fabric
Flow status | Model | Equation | R-Square |
---|---|---|---|
Laminar | GaussMod | a | 0.993 |
Transition | Bigaussian | b | 0.965 |
Turbulence | Exp3P1Md | c | 0.977 |
While the coloration fluid was in a transition flow status with the Reynolds number between 2300 and 4000, the dye uptake behavior on the silk substrate was decreased first and then improved with the increase of the Reynolds number, attaining the maximum
Theoretically, as for a fabric dyeing in an aqueous bath, the fluid flowing velocities between the bulk solution and the fluid layers close to the solid silk fabric as well as its fiber surfaces are continuously decreased and even almost reduced to zero, due to their namely called viscous forces. Generally, these viscous forces are produced from a series of molecular interactions between the water media and the solid surfaces of the substrate for a tight adsorption, and simultaneously from various internal friction resistances among those fluid layers. Therefore, there is a fluid layer or district adjacent to the solid surface of fabric in which the fluid flow velocity decreases from the bulk solution to those solid surfaces in dyeing bath, and is generally defined as hydrodynamic boundary layer (Zhao, 2009). Moreover, the fluid layer, which is very close to the fabric or fiber surfaces within the hydrodynamic boundary layer, is called diffusion boundary layer (Zhao, 2009). Generally, the dyeing fluid in a diffusion boundary layer is almost in a static state, the ions and/or molecules of dyes and auxiliaries mainly depend on their own thermal diffusion to penetrate this layer and then approach fabric and/or fiber surfaces for a subsequent adsorption to start an uptake procedure on the substrate. Therefore, in conventional coloration theory, the diffusion boundary layer is a barricade shield for mass transfer between the bulk solution and the substrate surface and presents remarkably effects on the uptake behavior and dyeing performance of dyes in bath.
Consequently, as for the laminar flow status, most of the acid dye molecules moved along a smooth straight-line paralleling to the pipe axis in various flow layers, and less or didn’t exhibit obvious irregular pulsations with the trajectory of the fluid micro mass, as shown in Scheme 1 (A). Moreover, there was mainly momentum transfer forward in the laminar flow for most of the dye molecules and less crosswise transfer between adjacent fluid layers in the coloration circular pipe. Consequently, only those of the acid dye molecules that were in the diffusion boundary layer could be transferred onto the fabric strip surfaces via their molecular thermal motions and then some attractions occurred for the acid dye adsorbs from the substrate macrochains before overcoming some repulsive forces between them. Accordingly, an appropriate increase of the Reynolds number in the laminar flow, namely a suitable improvement of the average velocity of the fluid flow, could lead to a reduction of the thickness of the diffusion barricade shield closely around the fabric strip. Thus, it was beneficial for some dye molecules from the hydrodynamic boundary layer or even the bulk solution to across the diffusion boundary layer, and reasonably resulted in the observed significant enhancement of the acid dye uptake behavior on the fabric strip. However, as the Reynolds number was higher than 1750 in the laminar flow, the acid dye uptake behavior was reversely decreased in some degree, although the diffusion boundary layer around the fabric trip surfaces continuously became thinner. It is probably due to the overhigh laminar flow velocity of the adjacent layers to the diffusion boundary layer, which could lead to a decreased across transfer for some of the acid dye molecules to the diffusion boundary layer via their limited molecular thermal motions. Therefore, although in the same laminar flow status, the
Transition flow status is a kind of flow status between laminar and turbulent flow, and the motions of fluid micro clusters are more complex than laminar and turbulent ones. When the dye fluid was in transitional flow status with a relatively small Reynolds number, the dye ions exhibited some stronger characteristics as in laminar flow status, and these characteristics also gradually decreased with the further increased Reynolds number, as shown in Scheme 1 (A). Additionally, the motion performance of the dye molecules was poor and there was no obvious mass transfer between adjacent flow layers. With the increase of Reynolds number, even if the diffusion boundary layer thickness on the fabric surface became thinner, the
When the coloration fluid was in turbulent flow, the
3.3 The dye uptake behaviors under different flow statuses by involving various pH values
In order to explore the characteristics of the acid dye uptake behaviors onto silk substrate under different flow statuses involving different initial pH values in the dyeing bath, a series of colorations were carried out at different dye bath pH values controlled by various Reynolds numbers in the fluid dynamics coloration machine. The achieved results are shown in Fig. 5.
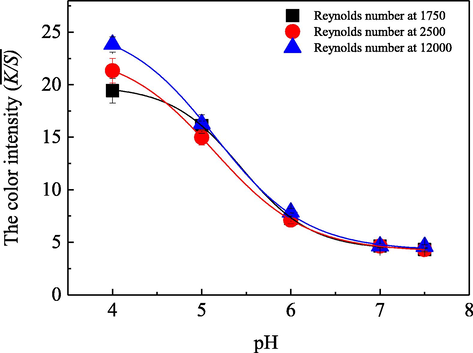
- Influence of solution pH value on the dye uptake behavior on silk fabric with the Renolds number at 1750 (■), 2500 (


Fig. 5 clearly shows that under various flow statuses, the
As well known, the silk fiber is composed of various amino acid molecules or their molecular residues, which contain a large amount of amino and carboxyl groups (Liu and Zhang, 2014). Therefore, as the pH value of the dyeing bath was lower than the isoelectric point of the silk fiber due to a large number of hydrogen ions (H+) presented in the dyeing bath, the ionization of carboxyl groups on the macro-chains of the fiber would be inhibited. Simultaneously, the positive ionizations of the primary amino and/ or imino groups (silk-NH3+, silk-(NH2+)-) would be occurred via the adsorptions of the free hydrogen ions (H+) in the dyeing bath onto silk fiber. Consequently, the silk fiber was positively charged, and the acid dye ions were also ionized into dye anions in the dyeing bath due to their connected sulfonic acid groups in molecules, which readily led to strong interactions, particularly Coulomb attractions, between the dye molecules or its anions and the positively charged silk fiber to form ionic bonds (He et al., 2019; Shin et al., 2008). Thus, various acid dyes could adsorb and uptake onto the silk fabric for coloration. Moreover, the lower the pH value of the solution was, the stronger the Coulomb force could be achieved between the acid dye ions and silk fiber, which accordingly caused more dye ions to adsorb and uptake on the surfaces of the substrate and resulted in the higher color intensity in Fig. 5. However, as the pH value increased, the concentration of H+ in the dyeing bath decreased while the concentration of OH– gradually increased which facilitated the ionization of the carboxyl groups and caused the fiber to be negatively charged. Thus, Coulomb repulsion forces between the fiber and the dye anions were not conducive to the adsorption and uptake of the dye molecules. Under this condition, the dye ions adsorbed to the fiber mainly by depending on hydrogen bonds and van der Waals forces. Therefore, as the pH value of the dyeing bath increased, especially from 4.0 to 7.0, the
As for the notable influences of the fluid flow statuses on the acid dye uptake behavior at a relative low pH value in the dyeing bath, as shown in Fig. 5, it was mainly relative to a fact that the adsorption of the dye ions onto the fiber predominantly depended on the Coulomb attractions, and was also relative to the diffusion boundary layers formed on the solid substrate. Generally, with the increase of Reynolds number, the diffusion boundary layer on the fabric surface became thinner, so the resistance of dye molecules to diffuse to the fabric surface decreased and they were easier to adsorb on the silk fabric. Particularly, under a relative low pH value condition, the strong coulomb forces as well as other attractions between the dye molecules and the silk fiber led to a very easy and high rate adsorption of the dye molecules which located very close to the substrate surface. Therefore, in this case, the adsorption and uptake rate and quantity of the acid dye onto silk fiber was mainly controlled by the dye transfer from the bulk solution to the solid substrate surface. Accordingly, with the increase of Reynolds number, namely with the fluid flow status changed from a laminar, or a transition flow to a turbulence flow, more acid dye molecules could be efficiently transferred to the fiber surfaces, which resulted in the corresponding improvements in the
However, with the increase of pH value in the dyeing bath, the coulomb attraction between the acid dye ions and fabric macromolecules gradually changed to coulomb repulsion. Even the weak interactions of the hydrogen bonds and van der Waals forces between the acid dye ions and fabric macromolecules became the main driving forces for the dye adsorption and uptake. Therefore, in this situation, the dye adsorption and uptake became a little difficult due to the produced coulomb repulsion and the weak driving forces, and were controlled by the interactions between the acid dye molecules and the silk fiber rather than a dye transfer process. Consequently, with the increase of the pH value in the dyeing bath, the influences of the fluid flow statuses were gradually decreased and even almost disappeared with the pH value at 7.5.
3.4 The dye uptake behaviors under different flow statuses at various temperatures
Generally, the transfer and uptake behaviors of dye molecules changed significantly with the variations of system temperatures and bath media flow statuses. In order to explore the characteristics of the acid dye uptake behaviors onto silk substrate under different flow statuses at different coloration temperatures, a series of colorations were also carried out at different temperatures and various Reynolds numbers in the fluid dynamics coloration machine. The achieved results are shown in Fig. 6.
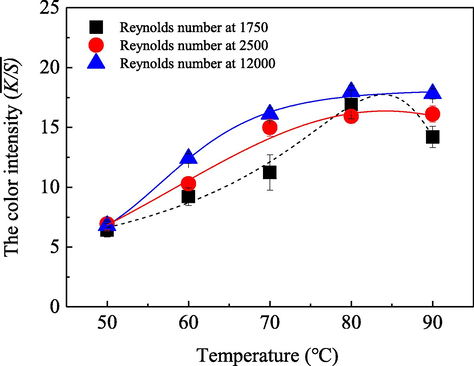
- Influence of the system temperature on the dye uptake behavior on silk fabric with the Reynolds number at 1750 (■), 2500 (


Fig. 6 demonstrates that very different characteristics and notable influences from the system temperature and the fluid flow status on the dye uptake behaviors and/or performances were observed with the temperature ranging from 50.0 °C to 90.0 °C. As shown in Fig. 6, with the dyeing temperature increased, the
Theoretically, with the increase of the dyeing bath temperature, the hygroscopic swelling of the hydrophilic silk fiber will be intensified significantly, thus many micro-gaps and tunnels among their macromolecules could be formed or increased and enlarged remarkably, which will be helpful and benefit for the dye molecules to diffuse into the fiber inner phases. Meanwhile, due to the increase of system temperature, the kinetic energies, movements and the diffusion rates of the dye molecules in fiber and bulk solution will be also improved greatly (Long et al., 2014; Zhao, 2009; Shin et al., 2008). Therefore, the
As for the influences of the fluid flow status, a relatively low dyeing temperature usually leads to a limited hygroscopic swelling of the silk fiber, and a relatively low molecular kinetic energy and poor diffusion behavior of the dye, so most of the dye molecules only adsorb on the surfaces of the fiber, which is a typical diffusion control process in the fiber at this situation. Therefore, very less differences and influences were observed as the three kinds of fluid flow statuses were applied in the dyeing bath at a system temperature of 50.0 °C. However, with the temperature increase, the notable and different influences of the fluid flow statuses on the dye uptake behavior were probably attributed to the fact that the micro masses in the laminar flow move along a smooth straight-line paralleling the pipe axis, and no or less transfer of the dye molecules between adjacent fluid layers, meanwhile, the diffusion boundary layer close to the substrate surface was very thick. Therefore, all the situations resulted in the relatively low uptake behavior of the acid dye on silk fabric as a laminar flow status with a Reynolds number at 1750 utilized in the dyeing solution. However, when the bath solution was in a non-laminar flow, such as the transition flow with a Reynolds number at 2500 and the turbulence flow with a Reynolds number at 12000, there is not only a momentum transfer occurred, but also heat and the dye molecules’ transfers simultaneously happen between their adjacent fluid layers. Thus, there were fewer or no parallel linear movements of the micro masses of the solution and the dye molecules against the fabric; on the contrary, the movements of most of them were chaotic along with the bath solution flow (Schlichting and Gersten, 2015), particularly for the turbulence flow status, as shown in the scheme 1. Therefore, more acid dye molecules were easily transferred along with the chaotic masses of the bath solution from the adjacent fluid layers to the simultaneously thinned diffusion boundary layers for adsorption and uptake, which accordingly resulted in more efficient improvements of the
3.5 The dye uptake behaviors under different flow statuses by involving various dosages of sodium sulfate
In order to explore the characteristics and the influences of the presence of a neutral salt, sodium sulfate which acts as a dyeing promoter in the dyeing bath, on the acid dye uptake behaviors under different fluid flow statuses, a series of dyeing experiments were further performed by employing various concentrations of sodium sulfate and different Reynolds numbers in the dyeing bath. The achieved results are shown in Fig. 7.
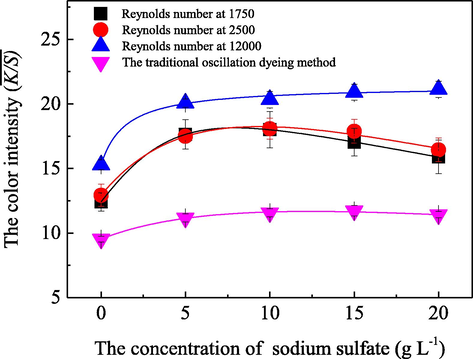
- Influence of sodium sulfate on the dye uptake behavior on silk fabric with the Renolds number at 1750 (■), 2500 (



Fig. 7 clearly shows that with the addition of the sodium sulfate in the coloration liquid with a concentration range over 0.0–5.0 g/L, the
Whether in laminar, transitional or turbulent flow, the concentration of Na+ in the dyeing bath increased greatly with the addition of sodium sulfate, which readily weakened or eliminated the coulomb repulsions between the acid dye ions and the fiber, and then reduced energy resistances for the dye ions to easily adsorb and uptake onto the surfaces of the fiber (Kamel et al., 2005). Therefore, as the concentration of sodium sulfate increased in an appropriate range, the
3.6 The dye uptake behaviors under different flow statuses by involving various applications of peregal O
For further exploring the characteristics and the influences of peregal O, a leveling dyeing auxiliary, on the acid dye uptake behavior on silk substrate under different flow statuses, a series of dyeing experiments were also investigated at different concentrations of peregal O and Reynolds numbers in the fluid dynamics coloration machine. The achieved results are depicted in Fig. 8.
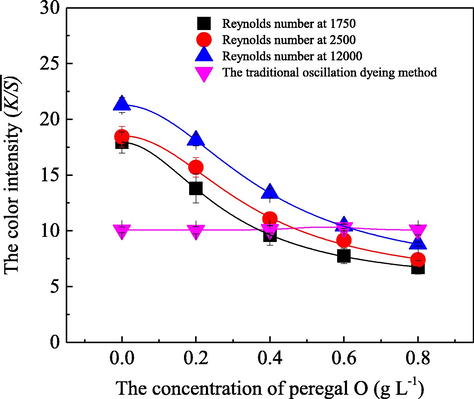
- Influence of peregal O on the dye uptake behavior on silk fabric with Reynolds number at 1750 (■), 2500 (



Fig. 8 clearly demonstrates that with the increase of peregal O concentration in the dyeing bath, the
Theoretically, peregal O is a typical nonionic dyephilic auxiliary leveling agent, which can dissolve and combine with the dye molecules via hydrogen bonds and van der Waals force in the dyeing bath. Therefore, various complexes, micelles, and/or more aggregations, bigger microclusters could be formed via those interactions between the acid dye molecules and the peregal O along with its increasing additions in the dyeing bath, which resulted in a decrease in the amount of the free monomolecular acid dye in the dyeing bath. Therefore, the dye ions adsorbed to the silk fabric decreased, and accordingly the
Additionally, as a nonionic surfactant, peregal O can reduce the surface tension of the dyeing liquid. When the concentration of peregal O is below its critical micelle concentration, the surface tension of the dyeing liquid would decrease with the peregal O concentration, which was conducive to the infiltration of the silk fabric and diffusion of dye ions (Sawada et al., 2004; Xie et al., 2011). Therefore, whether in laminar, transition, turbulence flow or the traditional oscillating dyeing, the
3.7 Color fastness performance of dyed silk fabric under different flow statuses
To further explore the characteristics and the influences of the coloration fluid flow statues on the acid dye color fastness on silk substrate, a series of coloration experiments and tests were performed at different flow statuses controlled by various Reynolds numbers in the fluid dynamics coloration machine. The achieved results are shown in Table 2.
Different coloration conditions | Washing fastness | Rubbing fastness | |||||||
---|---|---|---|---|---|---|---|---|---|
Fading | Staining | Dry | Wet | ||||||
Wool | Acrylic | Polyester | Nylon-66 | Cotton | Acetate | ||||
Re = 1750 | 4 | 5 | 5 | 4–5 | 4–5 | 4 | 5 | 4 | 4 |
Re = 2500 | 4–5 | 5 | 5 | 4 | 4 | 4–5 | 5 | 4–5 | 4–5 |
Re = 12000 | 4 | 5 | 5 | 5 | 5 | 4 | 5 | 4 | 4 |
Conventional dyeing | 4–5 | 5 | 5 | 5 | 5 | 4–5 | 5 | 5 | 4 |
a: a dosage of the acid dye at 0.05 g/L, an application of Anhydrous sodium sulfate at 5.0 g/L and an initial pH value of the bath solution at 5.0 with a total volume of 200 L. and a coloration temperature of 80.0 °C for 30 min duration.
Table 2 shows that a good, commercially acceptable color fastness under standard washing conditions was achieved with grades of 4 or higher grades for all the dyed silk substrates whether under laminar, transition or turbulent flow, especially for their fading and staining fastness on the six-fiber (cotton, wool, acrylic, polyester, polyamide-66, and acetate) standard adjacent fabric SDC Multifibre DW. Moreover, under dry or wet conditions, a good rubbing fastness more than 4 grades was also obtained for the dyed silk fabric under all the flow conditions. These results indicate that there was no obvious influence on the color fastness from different flow statuses in the dyeing bath, as well as from the traditional oscillation dyeing method. Moreover, these results also disclose that the self-built fluid dynamics coloration machine is useful and helpful for the investigation of the different influences of various fluid flow statuses on the dye uptake behaviors onto fiber substrates, etc.
4 Conclusions
To investigate and then control an appropriate dye uptake behavior under different coloration fluid flow statuses is a basic, direct and efficient method to improve the mass and heat transfer for coloration, particularly for product qualities and implementing sustainable processes. The results in this work show that a novel methodology and a novel special fluid dynamics coloration machine were successfully developed and applied to explore dye uptake behaviors in different flow statuses. The uptake behaviors of the acid dye on silk substrate were significantly different in the laminar, the transition and the turbulence flow, and their
Acknowledgements
The authors acknowledge gratefully the financial supports from the Six Talent Peaks Project in Jiangsu Province (Grant No. 2016-JY-057), and the Opening Project of Jiangsu Engineering Research Center of Textile Dyeing and Printing for Energy Conservation, Discharge Reduction and Cleaner Production(ERC-CN, China (Grant No. 2021-ERC-CN-Q811580621).
Declaration of Competing Interest
The authors declare that they have no known competing financial interests or personal relationships that could have appeared to influence the work reported in this paper.
References
- Adeel, S., Rehman, F.-u.-., Hameed, A., Habib, N., Kiran, S., Zia, K.M., Zuber, M., 2020. Sustainable extraction and dyeing of microwave-treated silk fabric using arjun bark colorant. Journal of natural fibers 17(5), 745-758. https://doi.org/10.1080/15440478.2018.1534182.
- Afzal, A., Samee, A.D.M., Razak, R.K.A., Ramis, M.K., 2020. Steady and transient status analyses on conjugate laminar forced convection heat transfer. Archives of Computational Methods in Engineering 27(1), 135-170. https://doi.org/ 10.1007/s11831-018-09303-x.
- Annus, I., Koppel, T., 2011. Transition to turbulence in accelerating pipe flow. J. Fluids Eng.-Trans. ASME 133(7), 9. https://doi.org/ 10.1115/1.4004365.
- Influence of silk surface modification via plasma treatments on adsorption kinetics of lac dyeing on silk. Text. Res. J.. 2013;83(3):288-297.
- [CrossRef] [Google Scholar]
- Effect of salts on water viscosity in narrow membrane pores. J. Colloid Interface Sci.. 2003;264(2):452-457.
- [CrossRef] [Google Scholar]
- An adsorption and kinetic study of lac dyeing on silk. Dyes Pigm.. 2005;64(3):231-241.
- [CrossRef] [Google Scholar]
- Chen, L., Caro, F., Corbett, C.J., Ding, X., 2019. Estimating the environmental and economic impacts of widespread adoption of potential technology solutions to reduce water use and pollution: Application to China's textile industry. Environmental Impact Assessment Review 79. https://doi.org/ 10.1016/j.eiar.2019.106293.
- Kinetics of dye sorption: effect of dyebath flow on dyeing uniformity. Am. Dyestuff Reporter. 1995;84(1):38-43.
- [Google Scholar]
- Synthesis of a novel disperse reactive dye involving a versatile bridge group for the sustainable coloration of natural fibers in supercritical carbon dioxide. Adv. Sci.. 2019;6(1):1801368.
- [CrossRef] [Google Scholar]
- Guha, A., 2008. Transport and deposition of particles in turbulent and laminar flow. Annual Review of Fluid Mechanics(40), 311-341. https://doi.org/ 10.1146/annurev.fluid.40.111406.102220.
- Guo, Q., Chen, W.g., Cui, Z.h., Jiang, H., 2020. Reactive dyeing of silk using commercial acid dyes based on a three‐component Mannich‐type reaction. Coloration Technology 136(4), 336-345. https://doi.org/10.1111/cote.12471.
- A technical review of emerging technologies for energy and water efficiency and pollution reduction in the textile industry. J. Clean. Prod.. 2015;95:30-44.
- [CrossRef] [Google Scholar]
- Color stripping of reactive-dyed cotton fabric in a UV/sodium hydrosulfite system with a dipping manner at low temperature. Cellulose. 2019;26(6):4125-4142.
- [CrossRef] [Google Scholar]
- Sustainable color stripping of cotton substrate dyed with reactive dyes in a developed UV/K2S2O8 photocatalytic system. J. Taiwan Inst. Chem. Eng.. 2021;121:241-256.
- [CrossRef] [Google Scholar]
- Hughes, J.; Rhoden, F. 1969. A modified Ubbelohde viscometer for measurement of viscosity of polymer solutions. Journal of Physics E-Scientific Instruments 2(12), 1134-1135. https://doi.org/ 10.1088/0022-3735/2/12/446.
- Internal convective heat transfer of nanofluids in different flow regimes: a comprehensive review. Physica A. 2020;538
- [CrossRef] [Google Scholar]
- Kamel, M., El-Shishtawy, R.M., Yussef, B., Mashaly, H., 2005. Ultrasonic assisted dyeing: III. Dyeing of wool with lac as a natural dye. Dyes and pigments 65(2), 103-110. https://doi.org/ 10.1016/j.dyepig.2004.06.003.
- Krichevsky, 1985. The adsorption and diffusion of dyeing and printing process. Textile Industry Press, Beijing, China, pp 22-38.
- Library, W.P., 2017. Ministry of environmental protection of the people's republic of China. http://english.mee.gov.cn/include/iframetop/index.shtml.
- Fluid Mechanics. China: tsinghua University Press; 2013. p. :298-306.
- Microfiber pollution: an ongoing major environmental issue related to the sustainable development of textile and clothing industry. Environ. Dev. Sustain.. 2021;23(8):11240-11256.
- [CrossRef] [Google Scholar]
- Silk fiber—molecular formation mechanism, structure-property relationship and advanced applications. Oligomerization Chem. Biol. Compd.. 2014;3:69-102.
- [CrossRef] [Google Scholar]
- Investigations on the level dyeing of fabrics in supercritical carbon dioxide. J. Supercrit. Fluids. 2011;57(1):80-86.
- [CrossRef] [Google Scholar]
- Dyeing of cotton fabric with a reactive disperse dye in supercritical carbon dioxide. J. Supercrit. Fluids. 2012;69:13-20.
- [CrossRef] [Google Scholar]
- A novel plant for fabric rope dyeing in supercritical carbon dioxide and its cleaner production. J. Clean. Prod.. 2014;65:574-582.
- [CrossRef] [Google Scholar]
- Clean fixation of dye on cotton in supercritical carbon dioxide with a heterogeneous and phase transfer catalytic reaction. Dyes Pigm.. 2015;115:88-95.
- [CrossRef] [Google Scholar]
- Mahdi, M., Tuj-Zohra, F., Ahmed, S., 2020. Dyeing of shoe upper leather with extracted dye from acacia nilotica plant bark-An eco-friendly initiative. Progress in Color, Colorants and Coatings 14(4), 241-258. https://doi.org/ 10.30509/pccc.2020.166673.1074.
- Mansour, H.F., Heffernan, S., 2011. Environmental aspects on dyeing silk fabric with sticta coronata lichen using ultrasonic energy and mild mordants. Clean Technologies and Environmental Policy 13(1), 207-213. https://doi.org/ 10.1007/s10098-010-0296-2.
- Mullin, T., 2011. Experimental studies of transition to turbulence in a pipe. Annual Review of Fluid Mechanics 43, 1-24. https://doi.org/ 10.1146/annurev-fluid-122109-160652.
- Sustainable textile production: cleaner production assessment/eco-efficiency analysis study in a textile mill. J. Clean. Prod.. 2016;138:248-263.
- [CrossRef] [Google Scholar]
- On the lower critical Reynolds number for flow in a circular pipe. Fluid Dyn.. 2003;38(4):545-551.
- [CrossRef] [Google Scholar]
- The influence of pH, temperature and time on dyeing of silk fabric by black bean anthocyanin-rich extract as colorant. Prog. Color, Color. Coat. (PCCC). 2021;14(3):179-186.
- [CrossRef] [Google Scholar]
- Sawada, K., Ueda, M., Kajiwara, K., 2004. Simultaneous dyeing and enzyme processing of fabrics in a non-ionic surfactant reverse micellar system. Dyes and pigments 63(3), 251-258. https://doi.org/ 10.1016/j.dyepig.2004.03.006.
- Boundary Layer Theory. Germany: Springer; 2015. p. :30-48.
- Shin, Y.-S., Son, K.-H., Yoo, D.-I., 2008. Dyeing properties and color of silk fabrics dyed with safflower yellow dye. Journal of the Korean Society of Clothing and Textiles 32(6), 928-934. https://doi.org/ 10.5850/JKSCT.2008.32.6.928.
- Effect of some process parameters in enzymatic dyeing of wool. Appl. Biochem. Biotechnol.. 2003;111:1-13.
- [CrossRef] [Google Scholar]
- Eco-friendly approaches for dyeing multiple type of fabrics with cationic reactive dyes. J. Clean. Prod.. 2017;165:1499-1507.
- [CrossRef] [Google Scholar]
- Xie, K., Cheng, F., Zhao, W., Xu, L., 2011. Micelle dyeing with low liquor ratio for reactive dyes using dialkyl maleic acid ester surfactants. Journal of Cleaner Production 19(4), 332-336. https://doi.org/ 10.1016/j.jclepro.2010.10.006.
- Development of a special SCFX-AnB3L dye and its application in ecological dyeing of silk with supercritical carbon dioxide. J. CO2 Utiliz.. 2020;35:67-78.
- [CrossRef] [Google Scholar]
- Investigation of the influence of supercritical carbon dioxide treatment on meta-aramid fiber: thermal decomposition behavior and kinetics. J. CO2 Utiliz.. 2020;37:85-96.
- [CrossRef] [Google Scholar]
- Dyeing and Finishing Process and Principle. China: China Textile Press; 2009. p. :17-46.