Translate this page into:
Synthesis and plugging effect of inverse emulsion polymerization microspheres (OPME) for oil-based drilling fluids
⁎Corresponding authors at: Cooperative Innovation Center of Unconventional Oil and Gas, Wuhan 430100, China. cdxupeng@yangtzeu.edu.cn (Peng Xu), cjdxxmb@126.com (Mingbiao Xu)
-
Received: ,
Accepted: ,
This article was originally published by Elsevier and was migrated to Scientific Scholar after the change of Publisher.
Peer review under responsibility of King Saud University.
Abstract
It is difficult to seal oil-based drilling fluids in the large pore and micro-fracture formation, and there are few suitable materials for the oil phase with good sealing ability at present. In order to solve the problem of the lack of sealing ability of oil-based drilling fluids, acrylamide, 2-acrylamido-2-methylpropane sulfonic acid, and acryloyl morpholine were used as monomers, N'N-methylenebisacrylamide was used as a cross-linking agent, Span-80 and Tween-60 were used as emulsifiers, and 2,2′-azobis(2-methylpropionamidine) dihydrochloride was used as an initiator. Polymer microsphere emulsion OPME was synthesized by inverse emulsion polymerization. The structure of polymer microspheres was characterized by infrared spectroscopy, scanning electron microscopy, electron microscopy, H NMR, laser particle size analysis and thermogravimetric analysis. The optimal synthesis conditions were determined by the control variable method: the monomer ratio of acrylamide, 2-acrylamido-2-methylpropane sulfonic acid, and acryloyl morpholine was 45:20:15, the amount of emulsifier was 8%, and the reaction temperature was 55℃. The synthetic polymer microspheres were added to the oil-based drilling fluids to perform filtration and loss plugging at atmospheric pressure and high-temperature and high-pressure, as well as pore and artificial fracture core plugging evaluation. The evaluation results show that the permeability reduction rate of pore core can reach 82%, and that of fracture core can reach 100% by adding polymer microspheres with 3% dosage. Finally, the pressure transmission experiment proves that the addition of polymer microspheres can slow the pressure transmission and filtrate intrusion, and enhance the stability of wellbore. Therefore, polymer microspheres are a micron-level plugging agent with good compatibility and high performance with oil-based drilling fluids, and the 3% dosage can better seal the formation of large pores and micro-fractures, which has a good potential for field application.
Keywords
Polymer microspheres
Oil-based drilling fluids
Inverse emulsion polymerization
Plugging ability
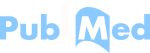
1 Introduction
With the shift of oil and gas development to deep stratum, deep-water and unconventional oil and gas, the large-scale use of oil-based drilling fluids is accompanied by a significant increase in wellbore strengthening. At present, the sealing materials and technologies for oil-based drilling fluids are mainly derived from water-based drilling fluids. There are many problems with the sealing effect and material oil compatibility. It is urgent to improve the sealing performance of oil-based drilling fluids to effectively reduce the hole wall strengthening problem and the resulting well leakage and other technical problems (Wang Zhonghua, 2011; Lin and Wang, 2014).
At present, effective leakage prevention and plugging are mainly achieved through physical plugging, and the plugging agents used for oil-based drilling fluids are rigid plugging agents and bitumen flexible sealing agents (Tang et al., 2017; Yue et al., 2006; Chen et al., 2022; Ma et al., 2019). Due to its poor deformability, conventional rigid plugging agents are difficult to effectively adapt to the formation with pores and micro-fractures, resulting in a poor sealing effect (Xu et al., 2016; Pourkhalil & Nakhaee, 2018). Asphalt flexible plugging agents have a strong adaptive ability, which can effectively solve the gradation problem between plugging materials and the size of the leakage channel, but their disadvantage is that their compressive resistance is limited, and the sealing performance will be affected to a certain extent (Lu et al., 2006; Zhao et al., 2021; Zheng et al., 2022). Since 2016, large oil service companies have started to study intelligent gel plugging technology, which has a high success rate at one time and is suitable for plugging while drilling without considering the gradation problem (Zhang & Liu, 2018; Peng & Yu, 2022; Zhang et al., 2010; Zhou et al., 2005). Gel microsphere is a deformable gel plugging material, which was first used as a displacement agent in the oilfield field to improve its recovery, and then became a plugging agent and a fluid loss reducer for water-based drilling fluids (Zhong et al., 2021; Magzoub et al., 2021; Li et al., 2021; Cao et al., 2015; Nie et al., 2019). However, hydrophilic gel microspheres cannot be directly used in oil-based drilling fluids because of their poor compatibility.
In view of this, in recent years, researchers have synthesized gel microspheres water-in-oil emulsion by a polymerization reaction and developed plugging agents suitable for oil-based drilling fluids. With the increase in good depth, Liu et al., 2016 using AM and AMPS as monomer raw materials, synthesized nano-micron scale spherical gels could not meet the demand of high temperatures, and could only resist the temperature of 80℃. DSP, a deformable plugging material for oil-based drilling fluids developed by (Al-Ajmi et al., 2018), was combined with calcium carbonate and elastic graphite to produce a specific drilling fluid system. The results of this system were applied to the Upper Zubeir and Latavi shales to effectively seal and prevent the intrusion of drilling fluid filtrate, but the particle size was about 200 nm, and smaller cracks cannot be effectively sealed. Zhong et al.,2018 synthesized an expandable polymer microspheres SPM through suspension polymerization. The plugging agent can absorb oil and expand and has good deformability and compressibility. However, the addition of SPM has a significant impact on the viscosity of oil-based drilling fluids. Xiang et al., 2020; Deng Zhengqiang, 2020 took acrylamide as the main synthetic monomer and synthesized gel microsphere emulsion OBMG by inverse emulsion polymerization. When the number of effective gel microspheres was 2%-3%, oil-based drilling fluids had the best sealing effect and could effectively seal micron cracks. Liu et al., 2021 synthesized a suspension of zwitterionic polymer gel microspheres with an average particle size of about 22 μm by suspension polymerization, which can seal the cracks in the size range of 5 ∼ 150 μm at high temperature, and the effect is better than that of oxidized asphalt and fine calcium carbonate. After hot rolling at 150℃, the plugging agent increases the apparent viscosity and plastic viscosity of oil-based drilling fluids by about 10 mPa·s, which has a great impact on the rheological property. Zhou et al., 2022 has developed a new cross-linked polymer microspheres P-90 for the Bohai Sea oilfield in China, which has good temperature resistance and good blocking properties for microporous membranes with pore sizes of 5 and 10 um. Liu et al., 2022 select p-styrene sodium sulfonate with benzene ring structure and sulfonic acid group to synthesize polymer microspheres with particle size of 2.82 ∼ 10.26um, which showed good filtration loss reduction performance in high salinity and high temperature environment.
Gel microspheres have the advantages of small size, good fluidity, good elastic deformation ability, etc., which can absorb water and expand under the condition of high temperature of the formation and squeeze into the rock holes under the action of pressure difference, so as to play a good sealing role. As a plugging agent in the field of water-based drilling fluids, polyacrylamide microspheres can squeeze into micropores through irregular deformation under the action of pressure difference. At the same time, they can absorb water and expand in the leakage channel, and form a compact pressurized sealing layer to improve the success rate of primary plugging (Yu & Jiang, 2011; Song et al., 2015; Wu Xiaole, 2014). Based on this, using the good elastic deformation ability of polymer microspheres, it is of great significance to develop a polymer microsphere plugging agent suitable for oil-based drilling fluids to solve the problem of nanometer pore and fracture gradation in formation.
2 Materials and methods
2.1 Monomer selection
The main synthetic monomers of polymer microspheres are acrylamide (AM), 2-acrylamido-2-methylpropane sulfonic acid (AMPS), acryloyl morpholine (ACMO), and N'N-methylenebisacrylamide (MBA):
-
Acrylamide (AM)
AM contains a carbon–carbon double bond and can be copolymerized with most vinyl monomers. It has active chemical properties. Because the branched chain contains only one amide functional group, it shows strong adsorption when synthesized.
-
2-acrylamido-2-methylpropane sulfonic acid (AMPS)
AMPS contains sulfonic acid groups, easy to copolymerize, and the reactivity rate of AM is similar, which can improve the rigidity of the main chain and enhance the temperature and salt resistance of the polymer.
-
Acryloyl morpholine (ACMO)
ACMO, as a new type of water-soluble polymeric monomer, has a rigid morpholine ring structure containing nitrogen, which can improve the thermal stability of the polymer. The monomer radical is more active when polymerized, and it is easier to react with other alkene monomers. Morpholine ring can increase the amide bond energy in the molecule and improve the temperature resistance of polymer (Huang et al., 2021).
-
N'N-methylenebisacrylamide (MBA)
The left and right ends of MBA each contain a carbon–carbon double bond, which can be used as a cross-linking agent to make the polymer form a network structure in the synthesis process, which can improve the thermal stability of the polymer.
2.2 Principles of polymerization
Polymer microspheres were synthesized by inverse emulsion polymerization, in which the monomer was dissolved in water and then dispersed in the oil phase with the help of an emulsifier to form a water-in-oil emulsion (Fig. 1). The polymer microspheres synthesized in oil-based drilling fluid have better compatibility than other conventional plugging materials and do not have the problem of greatly affecting the rheological properties of oil-based drilling fluids.Inverse emulsion polymerization process.
The reaction process of polymer microspheres is shown in Fig. 2. The amide groups provided by AM monomers are mainly responsible for the absorption and formation of backbone structures. The sulfonic acid group provided by AMPS could enhance water solubility, and the side group (CH3)2CH2SO3Na could enhance the rigidity of the molecular chain, thus improving the thermal stability of polymer microspheres. The morpholine ring provided by the ACMO monomer can improve the temperature resistance of polymer microspheres. The MBA monomer provides two double bonds that help form the network.Polymer microsphere synthesis process.
2.3 Experimental materials
Experimental drugs: acrylamide (AM), 2-acrylamido-2-methylpropane sulfonic acid (AMPS), acryloyl morpholine (ACMO), N'N-methylenebisacrylamide (MBA), 2,2′-azobis(2-methylpropionamidine) dihydrochloride (AIBA), sodium hydroxide, absolute ethanol, Span80, Tween60, analytical pure, China Shanghai Aladdin Biochemical Technology Co., ltd.; ammonium persulfate (APS), analytical purity, Tianjin North reagent, China; 3# white oil, industrial grade, China Jingzhou Jiahua Technology Co., ltd.
Experimental instruments: Even number display constant temperature magnetic stirrer (HJ-2B), Changzhou Gaode Instrument Manufacturing Co., ltd. Rotary viscometer, high temperature and high pressure filter, Qingdao Dream Instrument Co., ltd. Electronic thermostatic stainless steel water bath, Shanghai Yu Long Instrument Equipment Co., ltd., China; Optical microscope, Nanjing Jiangnan Yongxin Optical Co., ltd., China; Scanning electron microscope (SU8010), Hitachi, Japan.
The formula of oil-based drilling fluids for experimental evaluation: 80/20 oil–water ratio (3# white oil) + 4 % main emulsifier + 1 % auxiliary emulsifier + 2 % wetting agent + 2.5 % calcium oxide + saline (25 % mass volume concentration) + 2 % organic soil.
2.4 Polymerization steps
The preparation process of polymer microspheres OPME synthesized by inverse emulsion polymerization is as follows: 1) Configure the oil phase: add 120 mL of 3# white oil into a beaker and place it on a magnetic stirrer, add 15.9 mL emulsifier Span-80 during the stirring process, then stir continuously for 20 min. 2) Configure the aqueous phase: take 100 mL of deionized water and add AM, AMPS, and ACMO in the ratio of 45:20:15, then adjust the pH to about 7 using sodium hydroxide after the monomer has been completely stirred and dissolved. 3) Place the solution configured in 2) on a magnetic stirrer, add the cross-linking agent MBA 0.21 g and the emulsifier Tween-60 1.7 mL during stirring, and stir continuously for a further 10 min. 4) Place the oil phase on a magnetic stirrer and slowly pour in the aqueous phase while stirring, then add 0.14 g of initiator and finally keep stirring for 20 min to obtain the solution in an emulsion state. 5) Polymerization reaction: Pour the emulsion 4) into a three-mouth flask, put a stirrer in the middle of the flask, add nitrogen to one end for deoxygenation for 20 min, and turn on the water bath to heat the pot until the temperature rises to 55℃, and then turn on the stirrer for a reaction for 3 h, and finally get emulsion polymer microspheres OPME.
2.5 Structural characterization and performance evaluation
-
Infrared characterization of polymer microspheres structure. The quantitative emulsion was slowly dumped into absolute ethanol for washing and demulsification. After standing for a while, the precipitates were dried and crushed. According to the China standard GB/T 6040–2002 “General Principles of infrared Spectral Analysis Method Part 5: Sample preparation method”, the potassium bromide tablet method was adopted and the Fourier transform infrared spectrometer was used to characterize and analyze it.
-
The morphology of microspheres was observed under scanning electron microscope. The quantitative polymer microsphere emulsion was demulsified, washed, fully dried, and crushed. Then, according to the Scanning Electron microscopy method for Determination of micromorphology and Diameter of the China standard GB/T 36422–2018, the microsphere powder was taken for microscopic analysis by scanning electron microscopy.
-
Thermogravimetric analysis of the thermal stability of microspheres. A quantitative amount of microspheres powder was taken, the temperature was set at 28 ∼ 600℃, protected by an inert gas, the temperature increase rate was 10℃/min, and the thermal stability was studied using a differential heat-thermogravimetric simultaneous analyzer. The TG curves and corresponding data obtained from the experiments were analyzed in accordance with the China standard “NB/SH/T 0859–2013 Determination of thermal stability of chemical substances Thermal analysis method”.
-
High-temperature and high-pressure filtration loss measurement. According to the China standard GB/T 16783.2–2012 “oil and gas industry drilling fluid field test Part 2: oil-based drilling fluid”, the filtration loss of oil-based drilling fluids with polymer microspheres was measured after aging at 120℃×16 h, so as to determine the best synthesis condition of plugging agent.
-
H NMR analysis of polymer microspheres. The polymer microspheres are added to ethanol absolute, constantly stirred and demulsified, dried and crushed. Then according to the China standard GB/T 34247.2–2018 isobutene-isoprene rubber (IIR) unsaturation determination Part 2: Nuclear magnetic resonance hydrogen spectroscopy of polymer microspheres powder composition structure analysis.
-
Laser particle size analysis of polymer microspheres emulsion particle size. The polymer microspheres emulsion was added to the ethanol absolute solution for ultrasonic dispersion, and then the particle size of the polymer microspheres was analyzed according to the China standard GB/T 19077.1–2008 particle size analysis laser diffraction method Part I.
3 Results and discussion
3.1 Characterization
3.1.1 Infrared spectrum analysis of the OPME
According to the infrared spectrogram analysis of the synthesized product, 3422.065 cm−1 is the stretching vibration absorption peak of –NH2 in AM. The absorption peaks at 2928.377 cm−1 and 2856.06 cm−1 belong to the stretching vibration absorption peaks of –CH3 and –CH2-. The stretching vibration absorption peak of C⚌O in AM and MBA is at 1669.57 cm−1. The stretching vibration peak of the C—N group in AM and ACMO is at 1451.172 cm−1. The bending vibration absorption peak of -C(CH3)2- in AMPS is at 1360.051 cm−1. The asymmetric stretching vibration absorption peak of the sulfonic acid group is at 1183.597 cm−1. The stretching vibration absorption peak of -C—O—C- in ACMO is at 1041.372 cm−1. The analysis showed that the polymer microspheres contained the designed functional groups, which proved that the expected products were obtained by the inverse emulsion polymerization experiment.
3.1.2 H NMR analysis of the OPME
According to the H NMR analysis, δ3.5–3.8 (peak a) in the spectrum belongs to the proton absorption peak of the morpholine ring in ACMO. δ3.1–3.4 (peak b) belongs to the methylene proton absorption peak of group -CH2SO3-in AMPS; δ2.2–2.4 (peak c) belongs to the proton absorption peaks of the methyne of the main chain of the polymer microspheres; δ1.6–1.8 (peak d) belongs to the methylene –CH2- proton absorption peak on the polymer microspheres; δ1.1–1.3(peak e) belongs to the –CH3 in AMPS of the proton absorption peak. It can be seen that the samples prepared can be identified as polymers of AM, AMPS and ACMO by H NMR.
3.1.3 Light microscopic analysis of the OPME
In order to observe the overall distribution of polymer microsphere emulsion, a small amount of emulsion was dropped into the water and 3# white oil for dilution, and then the dilution liquid was dropped onto the slide, and the morphology and dispersion of polymer microspheres were observed under a 20 × 10 times light microscope (see Figs. 3 and 4).Infrared spectra of the OPME.
H NMR analysis of the OPME.
As shown in Fig. 5 (a), after dilution in water, the polymer microspheres showed a uniformly distributed spherical shape with a completely spherical shape; as shown in Fig. 5 (b), after dilution in 3# white oil, the polymer microspheres showed a droplet shape with overall uniform dispersion and uniform particle size. The results show that the polymer microsphere emulsions are insoluble in the water phase, but soluble in the oil phase without stirring, indicating that the polymer microspheres have good dispersion in the oil phase. This is mainly due to the fact that the microspheres are encapsulated inside the emulsion in the form of water-in-oil and the outer phase is the oil phase which can be better incorporated into oil-based drilling fluids with good mating properties.Microscopic view of the OPME after dilution in water and 3# white oil respectively.
3.1.4 SEM analysis of the OPME
Take a certain amount of polymer microspheres powder on conductive paper, after gold spraying treatment, put the sample into the sample chamber, and set parameters for determination, we can observe the microscopic morphology of the polymer microspheres at this time.
As can be seen from Fig. 6, the polymer microspheres are spherical in shape and uniform in size, averaging 1 μm ∼ 5 μm, which can be used as a plugging agent for oil-based drilling fluids with good grading properties for nano-micron pore joints in the formation.Electron microscopy of the OPME powder.
3.1.5 Laser particle size analysis of the OPME
The laser particle size analyzer was used to test the dispersed polymer microspheres emulsion, and the results were shown in Fig. 7. The particle size distribution range of the polymer microspheres was narrow, showing a single-peak distribution, indicating that the particle morphology was single and regular, and the main distribution range was 1.0 ∼ 5.0um, and it had good adaptability to the micron-level fractures in the formation (see Fig. 8).Laser particle size distribution map of the OPME.
Thermogravimetric analysis of the OPME.
3.1.6 Thermogravimetric analysis of the OPME
The OPME, as a plugging agent for oil-based drilling fluids, have high requirements for temperature resistance, and polymer polymers are easy to be degraded at high temperatures, so thermal stability must be tested by TG.
The thermogravimetric analysis of the synthesized products shows that the thermal decomposition of the polymer microspheres can be divided into three stages. 1) The first decomposition stage is between 28 ∼ 260℃, the TG curve of this stage decreases gently, which indicates that the mass of polymer microspheres is reduced by heat, mainly because the water absorbed by the sulfonic acid group and amide group in the synthesized polymer microspheres is evaporated by heating; 2) The second decomposition stage is between 260 ∼ 365℃, the TG curve of this stage decreases gradually, the mass of polymer microspheres is still 3) The third decomposition stage is between 365 and 463 °C, where the TG curve drops further, mainly because the main and side chains of the polymer microspheres also start to break and degrade, and their basic structure is destroyed. As a result, the amount of loss of polymer microspheres below 260 °C is low and meets the temperature resistance needs of most high temperature wells.
3.1.7 Preparation rate of the OPME
The emulsion of polymer microspheres synthesized quantitatively was taken and demulsified by constant stirring in the process of adding ethanol solution. After standing for 3 h, the operation was repeated twice, and the lower layer of precipitate was put into the dryer for 36 h to obtain solid particles of polymer microspheres and weigh them. The three measurement results are shown in Table 1 below. Preparation rate = solid particle mass of polymer microspheres after drying/emulsion mass of polymer microspheres × 100 %.
Weighing times
Quality of emulsions /g
Mass of solid particles /g
Preparation rate
/%
1
50
50
5018.93
37.86
2
19.11
38.22
3
18.87
37.74
It can be seen from Table 1 that the preparation rate of polymer microspheres is about 38 % in the results of three measurement experiments. In the actual synthesis process, the proportion of monomer is about 40 %, which is slightly higher than the preparation rate of polymer microspheres. The reason may be that some monomers did not fully participate in the reaction or generated other polymers in the synthesis process, or the loss may be caused by the process of removing the lower layer precipitation after demulsification of polymer microsphere emulsion, resulting in the reduction of particle mass at weighing and the calculated preparation rate.
3.2 Synthesis conditions optimization
3.2.1 Optimization of emulsifier dosage
During the polymerization reaction, the concentration of the emulsifier can have a significant effect on the viscosity and stability of the polymer microspheres emulsion. Therefore, as shown in Table 2, the amount of emulsifier was changed while other synthesis conditions remained unchanged, and carrying out the inverse emulsion polymerization reaction, the polymer microspheres with the optimum concentration were selected and added to the oil-based base slurry and aged at 120 °C × 16 h to analyze the emulsion-breaking voltage and high-temperature and high-pressure filtration loss of the oil-based drilling fluids.
Synthesis conditions
Various parameters
oil–water ratio
1.2:1
total monomer concentration
40 %
monomer ratio
45:20:15
initiator dosage
0.16 %
cross-linking agent dosage
0.24 %
reaction temperature
55℃
reaction time
3 h
It can be seen from Fig. 9 that the increase of emulsifiers will increase the emulsion-breaking voltage value of oil-based drilling fluids after aging, and the high-temperature and high-pressure filtration loss will significantly decrease. The low amount of emulsifiers makes the emulsifier molecules in the synthesis process unable to completely wrap all the dispersed phases, which will reduce the preparation rate of polymer microspheres. When the emulsifiers is added to oil-based drilling fluids, the content of the dispersed phase will increase, resulting in the low emulsion-breaking voltage and high-temperature and high-pressure filtration loss after aging. The increase in the number of emulsifiers can improve the emulsification effect and the stability of synthetic emulsion. When the emulsifier is added to oil-based drilling fluids, the emulsion-breaking voltage value increases significantly after aging, and the filtration loss of high-temperature and high-pressure gradually decreases, so it can effectively achieve plugging. When the amount of emulsifier is too high, the synthesized emulsion is relatively viscous and stratified obviously. The emulsion-breaking voltage value remains stable after the addition of oil-based drilling fluids and aging, and the filtration loss at high-temperature and high-pressure increases slightly. Therefore, the experiment shows that the optimum amount of emulsifier in the synthesis process is 8 %.Effect of the OPME synthesized with different emulsifier dosage on the emulsion-breaking voltage value and HTHP filtration loss of OBMs after aging (the monomer ratio of AM, AMPS and ACMO was 45, 20, 15, the reaction temperature of polymerization was 55℃, and the emulsifier dosage was 4%, 6%, 8% and 10% of the total mass).
3.2.2 Optimization of reaction temperature
In the polymerization process, the reaction temperature will affect the state of the emulsion, the synthesis rate of polymer microspheres, and the amount of preparation. Therefore, the reaction temperature was changed, but the other synthesis conditions were unchanged, the related parameters are listed in Table 3. After inverse emulsion polymerization, polymer microspheres with the best concentration were selected and added to the oil-based slurry. After aging at 120℃×16 h, the high-temperature and high-pressure filtration loss of oil-based drilling fluids were analysed (see Table 4).
Synthesis conditions
Various parameters
oil–water ratio
1.2:1
total monomer concentration
40 %
monomer ratio
45:20:15
initiator dosage
0.16 %
cross-linking agent dosage
0.24 %
emulsifier dosage
8 %
reaction time
3 h
Influence factor
Temperature /℃
Synthesis product status
reaction temperature50
Emulsion without stratification, yellow in color
55
Emulsion without stratification, light yellow in color
60
Emulsion with a small amount of lumpy gel
65
The emulsion has a lot of gel deposits
As can be seen from Fig. 10, the change in reaction temperature will have a significant impact on the state of the polymer microspheres emulsion, and lead to the reduction of the preparation rate. When the reaction temperature is lower than 55℃, the polymerization reaction rate will slow down and the synthesized products will decrease because the temperature required by the initiator is not reached. When the reaction temperature rises to 55℃, the preparation rate of polymer microspheres is greatly improved, and the emulsion does not appear delamination. When the emulsion is added to the oil-based drilling fluids, the filtration loss at high-temperature and high-pressure after aging is significantly reduced. As the reaction temperature continues to rise, the polymerization reaction rate is accelerated. Under the condition of constant stirring, the emulsion begins to demulsify, and a large number of agglomerated bulk gel precipitates and obvious stratification occur. As a result, the high-temperature and high-pressure filtration loss of oil-based drilling fluids with polymer microspheres increases after aging, and its plugging performance becomes weak. Therefore, the optimum reaction temperature was 55℃.Effect of the OPME synthesized at different reaction temperatures on the HTHP filtration loss of OBMs after aging (the monomer ratio of AM, AMPS and ACMO was 45, 20, 15, the emulsifier dosage was 8% of the total mass, and the reaction temperature of polymerization was 50℃, 55℃, 60℃, 65℃.).
3.2.3 Optimization of monomer ratio
In the process of polymerization, the number of functional groups on the molecular chain will be inconsistent with the different ratios of monomer, which will change the properties of polymer microspheres. Therefore, the ratio of monomer was changed, but other synthesis conditions remained unchanged, as shown in Table 5 below. After inverse emulsion polymerization, polymer microspheres with the best concentration were selected and added to the oil-based slurry. After aging at 120℃×16 h, the apparent viscosity, emulsion-breaking voltage value, and the high-temperature and high-pressure filtration loss of oil-based drilling fluids were analysed (see Tables 6 and 7).
Synthesis conditions
Various parameters
oil–water ratio
1.2:1
total monomer concentration
40 %
emulsifier dosage
8 %
initiator dosage
0.16 %
cross-linking agent dosage
0.24 %
reaction temperature
55℃
reaction time
3 h
Microsphere dosing/%
Before and after water drive
Flowing pressure/MPa
Liquid volume /mL
Time
/sPermeability
/10-3μm2
reduction rate of permeability/%
0original
0.40
2
78
3.83
42.3
0.36
2
85
after plugging
1.34
1
20
2.21
1.28
6
127
1original
0.60
2
56
3.60
52.2
0.62
4
105
after plugging
1.44
1
24
1.72
1.42
2
49
2original
0.64
3.5
102
3.20
61.3
0.62
2
60
after plugging
1.28
3
115
1.24
1.16
3
122
3original
0.62
4
121
3.25
82.5
0.54
8
265
after plugging
1.34
4.2
315
0.57
1.28
2
170
4original
0.50
4
121
3.93
66.2
0.48
2
63
after plugging
1.40
1
32
1.33
1.38
8
262
Microsphere dosing/%
Before and after water drive
Flowing pressure/MPa
Liquid volume /mL
Time
/sPermeability
/10-3μm2
reduction rate of permeability/%
0
original
0.04
1
27
112.54
66.3
0.02
4
207
after plugging
0.60
4
21
37.94
0.52
3
18
1
original
0.06
1
21
92.26
70.0
0.04
4
119
after plugging
0.30
2
27
27.64
0.12
4
153
2
original
0.08
2
34
88.79
85.4
0.06
1
22
after plugging
0.20
3.5
154
12.96
0.16
4
240
3
original
0.04
10
305
95.58
100
0.03
3
127
after plugging
1.50
0.1
966
0
1.34
0.1
1674
4
original
0.04
2
49
122.01
100
0.02
6
291
after plugging
1.52
0
2400
0
1.56
0
3600
According to (a) in Fig. 11, when polymer microspheres synthesized with different monomer ratios are added to oil-based drilling fluids, the measured apparent viscosity shows a slight upward trend before and after aging, and the range of change before and after aging is not obvious. It can be seen from Fig. 11(b) that the stability of the oil-based drilling fluids was destroyed after the synthetic polymer microspheres were added to it, and the emulsion-breaking voltage measured before aging gradually decreased. After aging at 120℃×16 h, polymer microspheres produced good compatibility with oil-based drilling fluids, reflecting certain temperature resistance performance. The emulsion-breaking voltage of oil-based drilling fluids measured gradually increased and tended to be stable, and it could be observed from the figure that the difference between emulsion-breaking voltage before and after aging was significantly reduced. Therefore, the proportion of AM monomer added gradually increases, so that the number of groups on the molecular chain of polymer microspheres increases, which is conducive to improving the stability of the emulsion.Effects of the OPME synthesized with different monomer ratios on the apparent viscosity and emulsion-breaking voltage of OBMs before and after aging (the reaction temperature of polymerization was 55℃, the emulsifier dosage was 8% of the total mass, and the monomer ratio of AM, AMPS and ACMO was 35:30:15, 40:30:10, 45:20:15, 50:20:10).
As can be seen from Fig. 12, when the percentage of AM monomer addition is relatively small, the preparation rate of polymer microspheres will be reduced, and when they are added into oil-based drilling fluids, the high-temperature and high-pressure filtration loss after aging is large and the sealing performance is relatively poor. As the percentage of AM monomer addition gradually increases, the high-temperature and high-pressure filtration loss after aging show a trend of first decreasing and then slightly increasing. This is mainly due to the poor temperature resistance of AM itself, which reduces the temperature resistance of the synthesized polymer microspheres, thus making the sealing performance of the oil-based drilling fluids weaker. Therefore, experiments show that the optimum monomer ratios for AM, AMPS, and ACMO are 45:20:15.Effect of the OPME synthesized with different monomer ratios on the HTHP filtration loss of OBMs after aging (the reaction temperature of polymerization was 55℃, the emulsifier dosage was 8% of the total mass, and the monomer ratio of AM, AMPS and ACMO was 35:30:15, 40:30:10, 45:20:15, 50:20:10).
3.3 Performance evaluation of the OPME
The polymer microspheres emulsion was synthesized according to the best synthesis conditions, namely, the ratio of AM, AMPS, and ACMO monomer was 45:20:15, the amount of emulsifier was 8 %, and the reaction temperature was 55℃. Synthetic polymer microspheres were added to the base slurry of oil-based drilling fluids and the plugging performance was evaluated. Oil-based base slurry formulation: 80/20 oil–water ratio (3# white oil) + 4 % main emulsifier + 1 % auxiliary emulsifier + 2 % wetting agent + 2.5 % calcium oxide + saline (25 % mass volume concentration) + 2 % organic soil + polymer microspheres in different concentrations.
3.3.1 Effect of the OPME addition on filtration loss
After the oil-based drilling fluids is prepared according to the formula, the temperature is set to 120℃ when using the roller and high-temperature and high-pressure water loss meter, and the comparison before and after observation and evaluation of its performance is made.
As can be seen from (a) in Fig. 13, since the synthesized emulsion only contains a certain effective amount of polymer microspheres, the oil–water ratio of oil-based drilling fluids will decrease with the increase of the concentration of microspheres so that the apparent viscosity and dynamic shear force before and after aging show an upward trend. As can be seen from (b) in Fig. 13, some monomers may not fully participate in the reaction or generate other polymers in the polymerization process, and the preparation rate of microspheres will be affected to a certain extent. Adding polymer microspheres with different concentrations to oil-based drilling fluids will increase the content of its dispersed phase, resulting in the reduction of emulsion-breaking voltage before and after aging.Effects of the OPME with different concentrations on the apparent viscosity, dynamic shear force, and emulsion-breaking voltage of OBMs before and after aging (the monomer ratio of AM, AMPS and ACMO was 45:20:15, the emulsifier dosage was 8% of the total mass, and the reaction temperature was 55℃).
As can be seen from Fig. 14, with the increase of polymer microspheres, the atmospheric and high-temperature and high-pressure filtration losses of aging oil-based drilling fluids gradually decrease, indicating that polymer microspheres have good compatibility with oil-based drilling fluids and can achieve effective plugging. The API atmospheric pressure test results showed that when polymer microspheres with 3 % content were added to the oil-based drilling fluids, the filtration loss after aging was only 1.8 mL. However, in the API test, the difference in filtration loss between the oil-based drilling fluid groups was not significant, and errors could not be ruled out. i.e. high-temperature and high-pressure experiments were conducted. Since the experimental temperature reached 120 °C, the upper pressure was set to 4.2 MPa and the back pressure was added to 0.7 MPa. The results of the whole set of experiments showed that the oil-based drilling fluids with 3 % content of polymer microspheres had the lowest high-temperature and high-pressure filtration loss after aging, and had the good temperature and pressure resistance and sealing effect. In conclusion, the optimum amount of polymer microspheres in oil-based drilling fluids is 3 %.Effect of different concentrations of the OPME on API filtration loss and HTHP filtration loss of OBMs after aging (the monomer ratio of AM, AMPS and ACMO was 45:20:15, the emulsifier dosage was 8% of the total mass, and the reaction temperature was 55℃).
3.3.2 Effect of the OPME addition on the permeability of pore cores
A 2.5 cm × 2.5 cm core was made with a block of cement, sand, and water ratio of 1:5:1. The permeability of the core before and after being driven into the oil-based drilling fluids was measured using a fluid measurement device (shown in Fig. 15), and then the effectiveness of different concentrations of polymer microspheres in sealing the pore core was judged based on the magnitude of the difference between the before and after values.Fluid measurement set-up (pore cores placed in core gripper).
As can be seen from Fig. 16, after the oil-based drilling fluids with different concentrations of polymer microspheres is driven into the pore core, the water drive is performed again and the permeability decreased significantly compared with the first water drive, while the difference in permeability between the two water drives can also be seen in the green area of the figure, At 3 % of microspheres, the difference in permeability between the front and rear water drive is the highest and the reduction rate of permeability reaches 82.5 %. In summary, the optimum amount of polymeric microspheres in oil-based drilling fluids is 3 %.Effect of different concentrations of the OPME added to OBMs on the permeability and reduction rate of permeability of pore cores (the polymer microspheres emulsion of 0, 1%, 2%, 3%, 4% concentrations was added to the OBMs).
3.3.3 Effect of the OPME addition on the permeability of fracture cores
The fluid measurement device was used to measure the permeability change of the 5.0 cm × 2.5 cm artificial fracture core after being driven into the oil-based drilling fluid, as shown in Fig. 17. The magnitude of the difference can evaluate the sealing performance of different concentrations of polymer microspheres on the artificial fracture core.Fluid measurement set-up (artificial fracture cores placed in core gripper).
As shown in Fig. 18, when oil-based drilling fluids with different concentrations of polymer microspheres was added into the artificial fractured core for water flooding again, the permeability could be observed to be significantly lower than that of the first water flooding, and it could also be seen from the figure that the permeability gradually increased in the blue area where the difference between the two water floods was observed. At 3 % and 4 % microspheres, the permeability of the second water drive was reduced to almost zero and the reduction rate of permeability was 100 % in both cases. In summary, the optimal addition of polymer microspheres in oil-based drilling fluids is 3 %.Effect of different concentrations of the OPME added to OBMs on the permeability and reduction rate of permeability of fracture cores (the polymer microspheres emulsion of 0, 1%, 2%, 3%, 4% concentrations was added to the OBMs).
3.3.4 Effect of the OPME addition on pressure transmission
Using a pressure transmission device (shown in Fig. 19), low permeability artificial core was used as the filtration medium, and then a pressure difference was established above and below the core, keeping the pressure at the upper end of the core constant (set the temperature at 80 °C, the confining pressure at 7 MPa, the upstream pressure of the core at 4.7 MPa and the downstream pressure at 0.69 MPa, achieving a difference pressure of 3.5 MPa between the top and bottom). The plugging performance of the polymer microspheres was evaluated by measuring the change of the lower pressure after the oil-based drilling fluids with different concentrations of polymer microspheres entered the core.Pressure transmission set-up.
As can be seen from Fig. 20, when the oil-based drilling fluids without polymer microspheres was conducting the pressure transmission experiment, the downstream pressure would increase instantaneously, and the rate of increase was large. The downstream pressure reached the equilibrium state around 10 h, and the equilibrium pressure was about 83.23 % of the pressure difference. With the addition of polymer microspheres of different concentrations, the pressure increase amplitude and rate decreased, and the equilibrium pressure accounted for 68.04 %, 56.80 %, 43.98 % and 43.19 % of the pressure difference, respectively. This indicates that the addition of polymer microspheres reduces downstream pressure and leads to slow pressure transfer, effectively sealing microfractures in the artificial core.Effect of the OPME addition on pressure transmission (the polymer microspheres emulsion of 0, 1%, 2%, 3%, 4% concentrations was added to the OBMs).
4 Conclusion
A polymer microsphere with good compatibility with oil-based drilling fluids was synthesized by inverse emulsion polymerization using AM, AMPS, ACMO, and MBA as the main monomers. The polymer microspheres were characterized by infrared spectroscopy, scanning electron microscopy, H NMR, laser particle size analysis and thermogravimetric analysis. The results showed that the size of the synthesized polymer microspheres averaged 1.0 ∼ 5.0 μm, were uniformly dispersed and spherical, contained the corresponding functional groups, and had good thermal stability. The performance of the polymer microspheres was evaluated by adding them to oil-based drilling fluids: the API normal pressure filtration loss and high-temperature and high-pressure filtration loss were reduced to 1.8 mL and 8.2 mL, respectively, when the microspheres were added at 3 %; the fluid testing experiments were carried out with two different cores to record the change in permeability before and after the oil-based drilling fluids was driven in. The data showed that the best sealing performance was achieved with the addition of 3 % microspheres. Then, pressure transmission experiments were used to demonstrate that the incorporation of polymer microspheres can lead to slow pressure transmission and effectively seal microfractures in artificial cores. Therefore, polymer microspheres can be used as a plugging agent for oil-based drilling fluids to solve the problem of nano-micron pore grade.
Declaration of Competing Interest
The authors declare no conflict of interest.
CRediT authorship contribution statement
Baimei Dai: Data curation, Formal analysis, Methodology, Project administration, Writing – original draft. Peng Xu: Conceptualization, Resources, Supervision, Writing – review & editing. Mingbiao Xu: Supervision. Qisheng Jiang: Methodology. Qinglin Liu: Project administration. Siwei Wang: Resources.
Acknowledgments
This research was supported by the Open Foundation of Cooperative Innovation Center of Unconventional Oil and Gas, Yangtze University (Ministry of Education & Hubei Province), UOG2022-02 and UOGBX2022-02.
References
- Al-Ajmi, A. , Al-Rushoud, A. , Gohain, A. , Khatib, F. I. , & Scolari, A. . 2018. Commingle Zubair Shale Sand Sequences by Using Deformable Sealing Polymer in Customized Drilling Fluid, Case Histories from Kuwait. Offshore Technology Conference Asia.
- Research and application of polymeric gel plugging agents. Contemporary Chemistry. 2015;44(11):4.
- [Google Scholar]
- Advances in theory and technology for leak prevention and plugging of oil-based drilling fluids. Contemporary Chemical Research. 2022;12:162-164.
- [Google Scholar]
- Research on oil-based gel microspheres and water-based high-temperature cross-linked gel for leak plugging and leaky formation fracture width prediction technology. China University of Petroleum (Beijing)); 2020. Doctoral dissertation,
- Synthesis and properties of modified conjugated polymers with acryloylmorpholine. China Science and Technology Paper. 2021;12:1319-1323.
- [Google Scholar]
- Preparation of water-based gel microspheres and their application in leak plugging. Drilling and Completion Fluids. 2021;38(6):7.
- [Google Scholar]
- Advances and reflections on oil-based drilling fluid technology for shale gas in Sinopec. Petroleum Drilling Technology. 2014;04:7-13.
- [Google Scholar]
- Development and application of spherical gel composite plugging agent. Petroleum Drilling Technology. 2016;44(2):6.
- [Google Scholar]
- Preparation and Performance Evaluation of Polymer Microsphere as Drilling FluidFiltrate Additive. Oilfield Chemistry. 2022;01 115 + 27
- [CrossRef] [Google Scholar]
- Preparation and plugging performance of an amphoteric polymer gel microsphere. Drilling and Completion Fluids. 2021;38(4):7.
- [Google Scholar]
- Exploration on the evaluation method of the anti-collapse performance of bitumen-based treatment agents for drilling fluids. Drilling Technology. 2006;29(1):3.
- [Google Scholar]
- Research and application of oil-based drilling fluid plugging agents. Broken Block Oil and Gas Field. 2019;04:529-532.
- [Google Scholar]
- Gelation kinetics of pam/pei based drilling mud for lost circulation applications. J. Pet. Sci. Eng.. 2021;200(2):108383
- [Google Scholar]
- Investigation on plugging and profile control of polymer microspheres as a displacement fluid in enhanced oil recovery. Polymers. 2019;11(12)
- [Google Scholar]
- Research and application of chemical gel retaining wall plugging technology for drilling in fractured zone strata. Drilling Engineering. 2022;49(1):8.
- [Google Scholar]
- Effect of nano zno on wellbore stability in shale: an experimental investigation. J. Pet. Sci. Eng.. 2018;173
- [Google Scholar]
- Synthesis and performance evaluation of cross-linked polyacrylamide microspheres. Modern Chemistry. 2015;8:4.
- [Google Scholar]
- Research and application of strong plugging oil-based drilling fluid system. Exploration Engineering (Geotechnical Drilling Engineering). 2017;11:21-25.
- [Google Scholar]
- Progress in research and application of oil-based drilling fluids at home and abroad. Broken Block Oil & Gas Field. 2011;04:533-537.
- [Google Scholar]
- Synthesis and performance study of polyacrylamide copolymer microspheres. Tianjin University); 2014. Doctoral dissertation,
- Synthesis of gel microspheres by reversed-phase emulsion polymerization and evaluation of their plugging performance. Drilling and Completion Fluids. 2020;37(3):7.
- [Google Scholar]
- Progress study on the application of nano blocking agents in drilling fluids. Applied Chemistry. 2016;04:742-746.
- [CrossRef] [Google Scholar]
- Research progress on the application of polyacrylamide microspheres in oilfield dissection and water plugging. Advances in Fine Petrochemicals. 2011;12(7):4.
- [Google Scholar]
- Yue, Q. S., Xiang, X. J., Li, Z., Huang, K. W., Xie, K. J., Cui, Y. Z. & Nie, M. S., 2006. Research and application of plugging performance of oil-based drilling fluids. Drilling and Completion Fluids (05), 40-42+86.
- Zhang, J., Cao, X. Y., Li, Z. S., Wang, W., Lan, Z. S., Wang, P. & Wei, R. Q., 2010. Application of smart gel GD-1 mixing and plugging technology in gas wells in Jingbian oilfield. Drilling & Production Technology (S1), 156-158+13.
- Intelligent gel plugging technology and practice for deep water wells in the western South China Sea. China High-Tech. 2018;12:62-66.
- [CrossRef] [Google Scholar]
- Synthesis of Liquid Tall Oil Asphaltene Amide Resins and Evaluation of Filtration Loss Reduction Performance. Drilling and Completion Fluids. 2021;38(5):7.
- [Google Scholar]
- Zheng, X. H., Bassey, E. S. , & D, J. G., 2022. Evaluation of the Effects of Nano-asphalt on Drilling Mud Properties and Its Impact Shale Stability. Springer, Singapore. Springer, Singapore.
- Zhong, H. K., X, Z., Gao, X., Qiu, Z. S., Li, W., An, Z. J., & H, W. A., 2021.Filtration and structure of bentonite-β-cyclodextrin polymer microspheres suspensions: Effect of thermal aging time. Journal of Molecular Liquids. doi:10.1016/J.MOLLIQ.2021.116914.
- Minimizing the hthp filtration loss of oil-based drilling fluid with swellable polymer microspheres. J. Pet. Sci. Eng.. 2018;172
- [Google Scholar]
- Zhou, H. L., Zhang, Y. L., He, Y. F., & L, F. F., 2022. A Study on Profile Control and Flooding Performance of New Crosslinked Polymer Microspheres. Journal of Southwest Petroleum University(Science & Technology Edition).
- Application of ploymer gel plugging agent for water in water shutoff in oil field. Inner Mongolian Petrochemical Industry; 2005.